Here are a few cabs I turned out this past weekend…
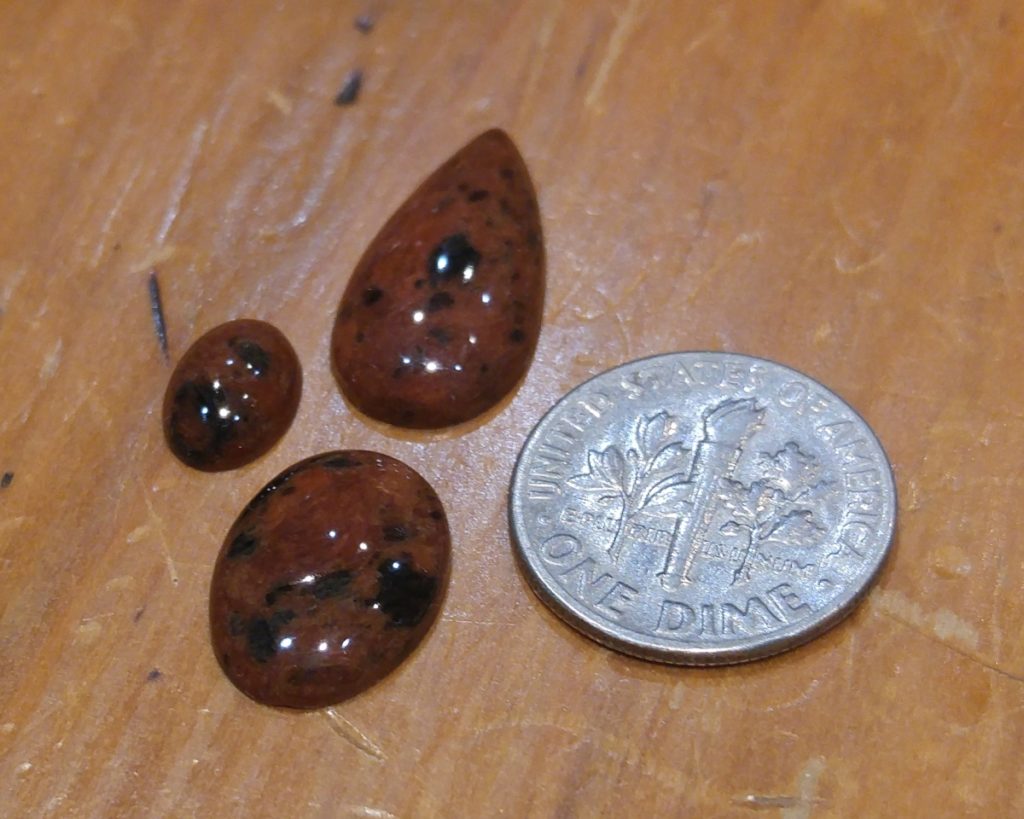
Mahogany Obsidian
First were some small ovals and a teardrop cab created from pieces that had broke off a 1/8″ slab of Mahogany Obsidian that I have. The “mahogany” color in the obsidian is due to hematite or limonite (iron oxide) mixed in with the silica, creating blotches or sometimes even flowing waves of the rusty color along with the black obsidian (which is usually made of up of minerals such as magnetite, hornblende, pyroxene, plagioclase and biotite).
As the slab was thin, either low-dome or small cabs are really the only choices I can make out of that material. And, as the slab had already fractured creating several smaller pieces, I used few of the smallest ones and made the cabs pictured above. I included a dime in the picture as a reference to give you an idea of their size.
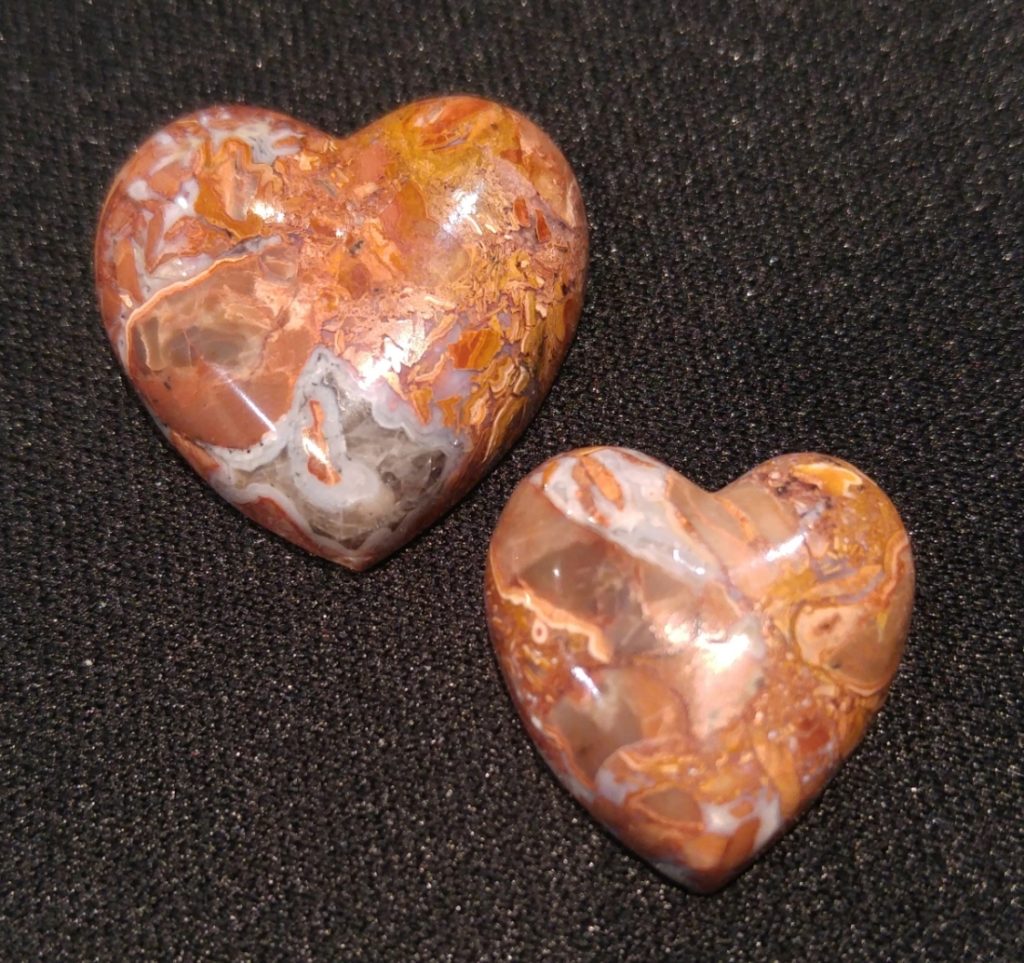
Butterfly Jasper Hearts
Above are a couple hearts I cabbed out of some Butterfly Jasper that is mined in Mexico. A pretty rock with brecciated jasper and quartz mixed throughout, the hearts were something Kathy had wanted me to give a shot at trying. I had never cabbed hearts before, though I knew how, so I was eager to give it a try myself. I was pleased that these turned out not bad at all! The top heart is 26x26mm, and the smaller bottom heart is 20x20mm.
One of the things that I had heard on various YouTube videos regarding the CabKing 6″ cabbing machine when I was doing my pre-purchase research was that the wheels were not spaced far enough apart to cab large stones, or work designs such as hearts (where you need to use the edge of the wheel for grinding/polishing the “V” in the heart). Yes, the CabKing 8″ machine spaces the wheels further apart, accommodating those needs quite well, but that does not mean the 6″ machine is not capable of working such material.
So, unless you are needing to frequently work large stones or create hearts and other designs that require working on the edge of the wheels, don’t think that it can’t be done on the 6″ machine (which is also a LOT lower in price than the 8″ machine). The trick? Use the additional wheel spacers supplied with your 6″ machine to take the place of one of the wheels when that extra space is needed.
It will take you a bit longer to work your stones of course, as you will need to swap out wheels to progress through the grits since you are working with just two wheels on an arbor at a time. But, it’s not a hard process to do, and doesn’t take that long, really. In working the obsidian, I forewent the 80-grit wheel and only formed the cabs lightly on the 220-grit wheel to keep any chipping to a minimum, then on to the 280-grit, so the “swapping-out” of wheels was only needed on the other arbor when it came time to cycle through the 600, 1200 and 3000-grit wheels.
If you only find yourself on occasion needing to work with large stones or designs that need more than the default 1/2″ spacing between the wheels as is normal with the 6″ wheel machine, a little swapping around with the wheels and included spacers can get you the room you need. Yes, it takes a little more work, but as these cabs demonstrate, it’s certainly do-able!